Transport in Porous Materials of XCT-based microstructures
Introduction Microstructure has a significant influence on the properties and durability of materials. Development of new 3D imaging investigation techniques opened a possibility to formulate models in the 3D geometries representing the microstructure of multiphase and porous materials. The work of our team focuses on preparation of 3D meshes representing materials’ microstructure which we further use in the numerical simulation of mass, energy and momentum transfers, i.e. pore-scale flow of molten metal in carbon refractory materials, multi-scale ion transport in cementitious materials and work of KCl/polymer reference electrodes and lithium-ion battieries. The 3D meshes are created based on the on the nano- and micro- X-ray computed tomography (XCT) measurements. Moreover, we use XCT measurements to evaluate influence of various degradation mechanisms on materials’ microstructure, based on the comparison of the exactly same volume, before and after degradation process. Additional field of our interest is determination of transport properties, e.g. effective diffusivity, tortuosity and constrictivity based on the measured 3D microstructures.
X-ray computed tomography In our work we focus on the X-ray computed tomography (XCT), which enables us to observe the 3D microstructure of different ceramic, polymer/ceramic and metal/ceramic materials, with a various spatial resolutions. Moreover, the method is non-destructive, which allow us to observe materials before and after degradation processes. The main process of XCT measurement is sample irradiation by X-rays, leading to creation of 2D radiograms, which are further used for reconstruction of material’s 3D microstructure. Most of our micro-XCT investigations are performed using Nanotom 180S (GE Sensing & Inspection Technologies GmbH), which work in the cone beam geometry (Fig. 1) and allow us to achieve spatial resolution up to 1 x 1 x 1 µm3. In measurements, which require higher spatial resolution (up to the 130 x 130 x 130 nm3) we use X-ray microscope, Xradia Ultra 100.
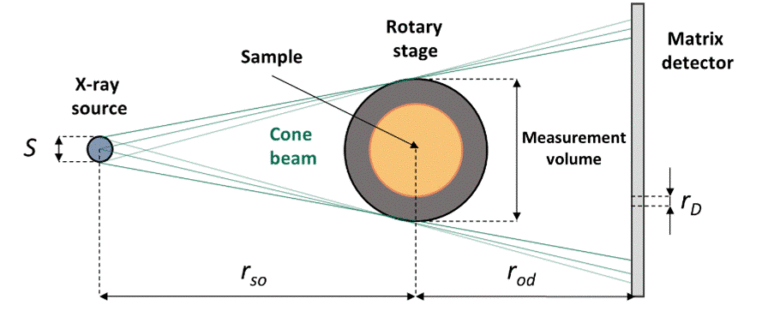
Fig. 1 Scheme of cone beam geometry X-ray computed tomography.
Geometry analysis and mesh generation In order to describe morphology and transport properties, measured XCT data is processed using open-source platform ImageJ with various plugins. We are able to perform phase segmentation, calculate volume fractions of each phase and determine several parameters describing morphology and transport properties i.e. total and continuous pore structures, local pore thickness distribution, geometrical tortuosity, constrictivity. Methodology of XCT data processing is presented in [1] and [4]. Essential part of our work is a preparation of 3D meshes for numerical simulations, which we do using two approaches. In first, we create 3D surface mesh of single phase using open-source software MeshLab. 3D surface meshes can be imported into simulation software, e.g. COMSOL Multiphysics and used to create 3D geometry for calculations. Details of the method are presented in [2]. In the second approach, we create 3D volumetric meshes representing multi-phase materials using Simpleware ScanIP software. Created mesh can be prepared for chosen simulation software. The example of XCT data, separated continuous pore structure and 3D geometry for calculations is presented in Fig. 2.
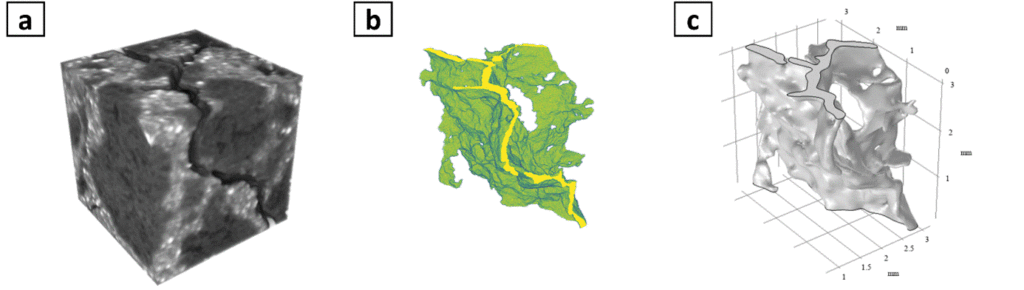
Fig. 2 Steps of mesh generation: a) measured XCT data, b) separated open pore structure and c) 3D geometry for pore-scale flow simulations.
Follow selected examples of projects carried out in our group.
Applications:
- Degradation of carbon refractory materials
- Multi-scale transport of ions in cementitious materials
- Determination of electrodes’ transport properties
Cooperation. Projects realized in cooperation with Fraunhofer IKTS, Dresden, Germany; deepXscan GmbH, Dresden, Germany; and the Faculty of Physics and Applied Computer Science AGH-University of Krakow.
Research papers:
- J.Stec, 3D pore structure and infiltration resistance of micropore carbon materials, Wydawnictwo Naukowe AKAPIT, Kraków (2020).
- J. Stec, J. Tarasiuk, S. Wroński, R. Filipek, Permeability of micropore carbon materials based on steady-state pore-scale flow calculations in real 2D and 3D microstructures, Ceramics international, 45, (2019), 17638-17645.
- J. Stec, J. Tarasiuk, S. Wroński, P. Kubica, J. Tomala, R. Filipek, Investigations of molten metal infiltration into micropore carbon refractory materials using X-ray computed tomography, Materials, 2021, under review.
- J. Stec, J. Tarasiuk, S. Nagy, R. Smulski, J. Gluch, R. Filipek, Non-destructive investigations of pore morphology of micropore carbon materials, Ceramics international, 45, (2019), 3483-3491.
- Jakub Stec, K. Kutukova, E. Zschech, Robert Filipek, The influence of capillary pores on transport of chloride ions – numerical simulations in nano-XCT based 3D cementitious microstructures, 9th European Nanoanalysis Symposium, October 9th, 2020.
- J. Stec, R. Filipek, Modeling of liquid flow through the porous materials of different microstructure, Cement Wapno Beton, 6, (2017), 489–506.
Contact: Prof. Robert Filipek