Degradation of Refractory Materials - the Inverse Problem
Introduction. The blast furnace process is a dominant technology in the constantly growing global steel production. Monitoring of refractory materials conditions during the blast furnace process is extremely difficult due to difficulties of direct measurements. One of the possibility is thermocouple measurements carried out at selected places inside refractories. Theoretical calculations, which allow to predic temperature distribution in the blast furnace hearth, became significant in the blast furnace process operations.
Mathematical model. A mathematical model capable of describing heat transport in the blast furnace combined with experimental readings of thermocouples for selected places in refractory allowed to formulate the inverse heat transfer problem. Complexity of this problem stemmed from the fact that the geometry of the blast furnace hearth consists of a several materials/phases with different properties, and in addition some of these phases can be consumed entirely. A solution of the inverse problem results in an estimation of the current state and wear of the blast furnace refractory lining. For the first time determination of shape for 3D geometry without the assumption of axial symmetry of blast furnace hearth has been performed.
Results. Computer simulations of temperature distributions were carried out using ANSYS Fluent software. In Fig. 1 the initial geometry (left) and the optimized geometry obtained using the inverse heat transport method in 2D geometry are compared.
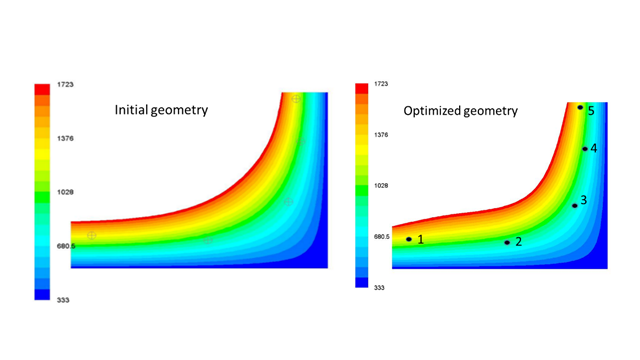
A 3D geometry of the blast furnace and available thermocouple positions for which temperature were measured are presented in Fig. 2.
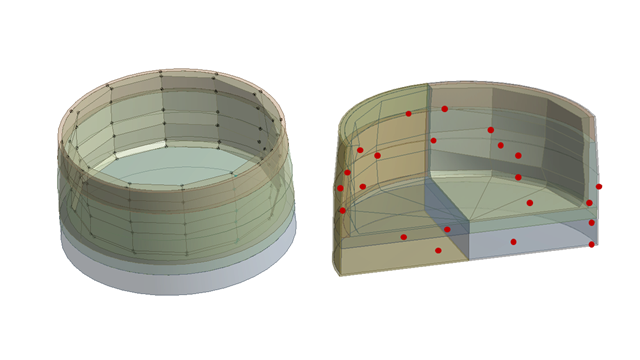
The inverse method for a real 3D blast furnace geometry was formulated and solved. The optimized geometry of the blast furnace hearth quarters – are presented in Fig. 3.
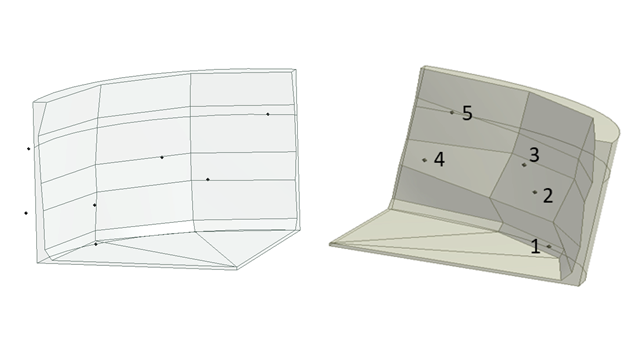
Cooperation. Project realized in cooperation with Tokai COBEX Polska.
Research papers:
- R. Filipek, “Modeling and inverse methods in materials engineering” – monograph, Wydawnictwo Naukowe “Akapit”, Kraków 2019.
- R. Filipek, K. Szyszkiewicz, “Inverse methods in corrosion research and materials degradation”, Ochrona przed Korozją, 60 (10), (2017), 358–363.
- K. Szyszkiewicz, P. Dziembaj, R. Filipek, “Heat transfer and inverse problems; selected cases in 1D and 3D geometries”, Archives of Metallurgy and Materials, 58 (1), (2013), 9–18.
- P. Dziembaj, Modelling of heat transfer in carbon based isolating materials – Shape determination of blast furnace hearth lining, PhD Thesis, AGH University of Science and Technology, Kraków, 2017.
Contact: Prof. Robert Filipek