Multiphysics Modelling - SHS Process Optimization
Introduction. Self-propagating high-temperature synthesis (SHS) was developed in the late 1960s and has been used to synthesize many ceramic materials including oxides, nitrides, carbides, and metal hydrides. In an SHS process, finely powdered reactants are pressed into a pellet and ignited on one side by an external heat source. After the ignition, the heat source is turned off because the SHS reaction is highly exothermic. The heat generated from the combustion is sufficient to sustain the reaction front to propagate through the pellet and convert reactants to products (Fig. 1). The fast combustion front movement (1–10 cm×s-1) enables a large-scale production in a short period of time. Fast cooling allows the formation of ceramic powders with very fine grains and metastable compounds.
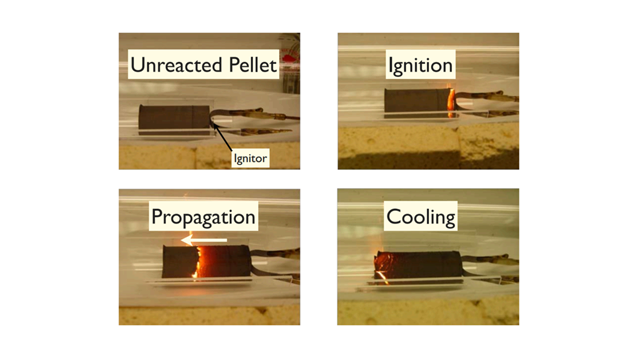
Mathematical model. The heat, momentum and mass transfers are taken into account to model the self-propagating high-temperature synthesis process. The model was formulated for an arbitrary 3D system geometry. Here for better visualization we consider an example 2D geometry presented in Fig. 2. The example geometry consists of a pellet 3 cm in length and 2 cm in width placed on alumina holder of 0.4 cm in thickness. The reaction system is placed inside the reaction chamber filled with argon.
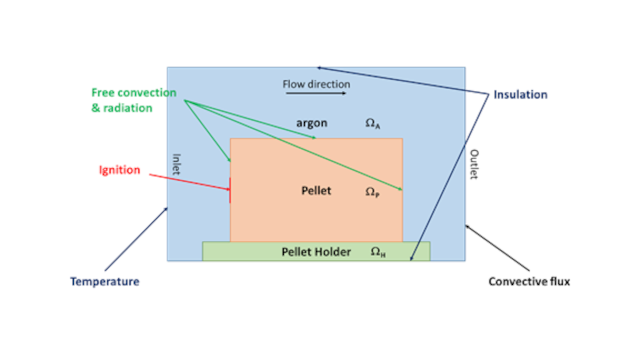
Cooperation. Project realized in cooperation with Department of Inorganic Chemistry at the Faculty of Materials Science and Ceramics AGH-University of Krakow.
Research papers:
- R. Filipek, “Modeling and inverse methods in materials engineering” – monograph, Wydawnictwo Naukowe “Akapit”, Kraków 2019.
Contact: Prof. Robert Filipek